Home
Authors Papers Year of conference Themes Organizations To MES conference
Analysis of the effect of membrane shape at mechanical strength and parameter stability of MEMS pressure sensors |
|
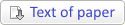 |
|
|
Authors |
| Vlasov A.I. |
| Tsivinskaya T.A. |
| Shakhnov V.A. |
Date of publication |
| 2016 |
|
Abstract |
| Topological synthesis of membranes for MEMS of sensors of pressure is an actual task. Use for these purposes of silicon is based on that the crystal lattice of silicon is cubic face-centered like diamond, but because of the bigger length of communication between atoms of Si-Si in comparison with communication length of C-C hardness of silicon is much less, than diamond. This fact does silicon more preferable material when developing sensitive elements for measurement of small mechanical deformations.
At production of control and measuring sensitive elements requirements to quality of silicon on all thickness of a plate raise. As a result of removal of a defective layer on a surface microdefects which will extend in depth of volume of material are formed. And superficial atoms of plates in comparison with volume have bigger quantity of nonsaturated chemical bonds, than the high adsorptive ability leading to pollution of a working surface speaks. Depending on a type of interaction of pollution with a surface distinguish physical and chemical absorption. Physical adsorption is a result of intermolecular electrostatic Coulomb interaction and a particle, making the thermal movements, possess a sufficient stock of energy to overcome forces of communication and to move, being removed from a surface or on the contrary on mechanical microdefects get to depth of material. Physically adsorbed pollutions are all types of mechanical particles, and also all types of organic materials connected with a surface by forces of physical adsorption belong. Different types of oxidic and sulphidic films on surfaces of plates, cations and anions of the chemicals applied in the course of cleaning of a surface of a plate belong to chemically adsorbed pollution.
METHODS
At production of sensitive elements for control and measuring sensors in volume of a crystal the working elements increasing sensitivity of a crystal to changes of size of the measured mechanical deformation are formed. In pressure sensors such working element is the membrane of square shape received by method of liquid anisotropic etching in volume of a crystal. The membrane size, size of the party of a square and thickness depend on the size of the measured pressure.
Anisotropic etching is based on a difference of speeds of etching of the different planes of single-crystal silicon. In most cases liquid anisotropic etchants represent the multi component solutions consisting of an oxidizer which oxidizes silicon to the hydrated silicon dioxide, and the complex basis intended for formation of a soluble complex ion and water. Shortcomings of this method are need of protection of a front surface, poor quality of all types of protection means at deep etching, probability of penetration of solution of etchanting on defects in the masking layer to elements of the sensor and their damage, formation of roughnesses on surfaces of etching and complexity of receiving a thin working membrane. The greatest number of microdefects is formed on border of thickness change of material and a bottom surface.
Modern techniques of 3D modeling allow to demonstrate subherbs and microdefects on a surface of a membrane and in a zone of fastening of a membrane. Results of calculations and modeling when carrying out control tests of a sensitive element for mechanical durability are confirmed: destruction of a membrane in all cases occur just on border of formation of a membrane and first of all in places of the maximum values of elastic deformations clearly visible.
Except the main zones of elastic deformations areas of elastic deformations the zones of etching, quantity and size of the dislocations created in the course of etching located on corners of a membrane and depending on correctness of geometry of contours are distinctly allocated.
Plasma and jet ionic etching are the most widespread types of dry etching. Besides the magnetron method of dry etching is discussed recently.
Orientation of a crystal at "dry" etching doesn't matter, chemical reactions are started by external energy in the form of high-frequency power with the lowered pressure in a chamber. In comparison with anisotropic plasma etching is less exact as depending on pressure and composition of gas, geometry of an electrode and the disseminated power. Small side subherbs can exist, but it can provide a form of an elastic element which is rather heavy for creating by means of anisotropic etching, for example, a round membrane. Smaller thickness of a working membrane is important when developing sensors on midget pressure with small overall dimensions. Also advantage is in high anisotropy of process and lack of need of carrying out additional operations for removal from a surface of products of reaction and the third-party impurity which are contained in initial reagents.
The form of a circle provides considerably smaller values of elastic deformations in the field of membrane border formation of a working membrane and the most important that these values are evenly distributed on a contour of a membrane and in membrane material.
Similar distribution of values of elastic deformation allows to consider the silicon membrane as the flat membrane fixed on a contour and loaded by pressure. Nature of deformation of a membrane depends on the size of deflections which it receives under loading. At small deflections, and in pressure sensors no more 0,15 mm, movements of a membrane arise generally as a result of the flexural deformations which are settling down between border of the main material of a crystal and the median plane. The median plane (the median plane is the plane equidistant from the crystal plane) membranes keeps the sizes in the field of small movements. Therefore, the area of the maximum values of elastic deformation remains invariable and therefore can't actively influence formation of dislocations in the field of a membrane exposed to flexural deformations. Conclusion is the membrane has the expressed straight-line characteristic. When calculating a membrane in the field of small movements it is possible to use the linear theory of a bend of round plates.
RESULTS
The round membrane, in view of lack of critical values of mechanical deformations on border of formation of a membrane, is capable to sustain big mechanical overloads, than square membrane, without additional design completions of a sensitive element.
Distribution of elastic deformations strictly on zones allows by method technological extra earnings to develop the universal technology allowing to neutralize influence of local dislocations in volume of silicon on an error of parameters of the sensor.
Distribution of elastic deformations is provided at condition of small movements the rectilinear characteristic of changes of tension from the measuring bridge of a sensitive element from change of pressure influencing a membrane.
Area of the maximum elastic deformations in the central part of a membrane when dropping loading from a membrane striving for balance of forces will promote return of a membrane to an initial state and by that to reduce a measurement error on reverse motion of a membrane.
Reduction in the course of production of a crystal of factors of the local centers of dislocations and microdefects influencing emergence in structure of material provides long-term stability of parameters of the sensor.
The accurate form of a circle allows to use the acquired methods of the mathematical analysis and calculation of optimum structures, from the point of view of ensuring working parameters of the sensor, the sizes of a membrane and calculation of the integrated circuit of transformation of mechanical deformation of a membrane to an accurate and stable electric signal. |
Keywords |
| single-crystal silicon, microdefects, mechanical deformations, a silicon membrane. |
Library reference |
| Vlasov A.I., Tsivinskaya T.A., Shakhnov V.A. Analysis of the effect of membrane shape at mechanical strength and parameter stability of MEMS pressure sensors // Problems of Perspective Micro- and Nanoelectronic Systems Development - 2016. Proceedings / edited by A. Stempkovsky, Moscow, IPPM RAS, 2016. Part 4. P. 65-70. |
URL of paper |
| http://www.mes-conference.ru/data/year2016/pdf/D084.pdf |
|
|